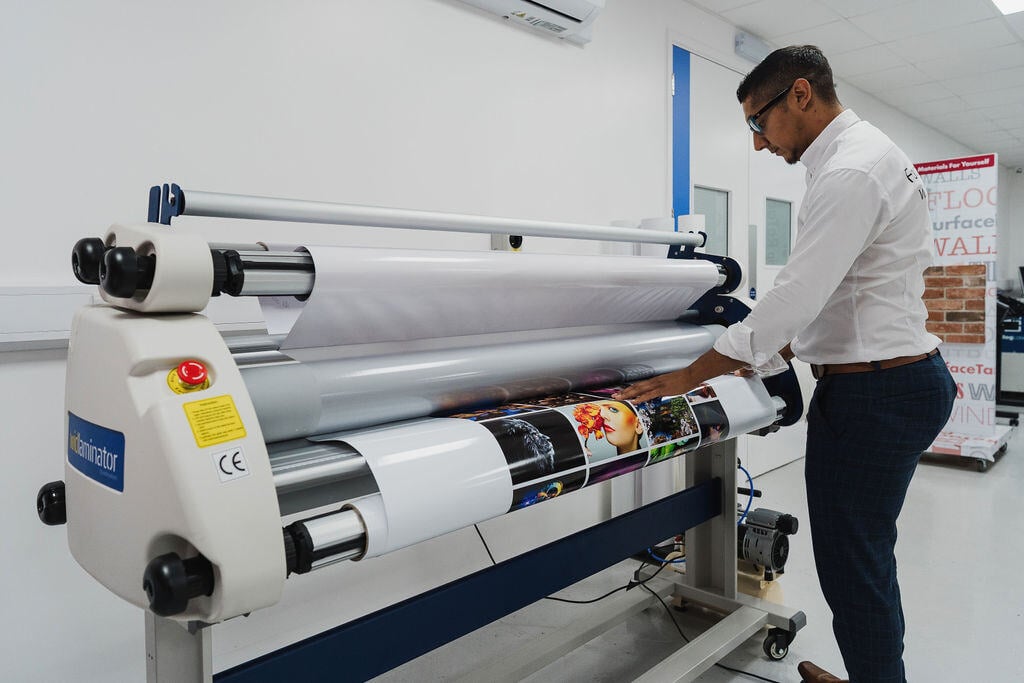
Best ways of utilising laminators for applying laminate films
This blog will explore the best ways of utilising laminators for applying laminate films. Lamination is a crucial step in the production process for many print businesses, ensuring that prints are protected, long-lasting, and visually enhanced.
What difference does a heated top roller make?
When it comes to wide-format laminators, print businesses often find themselves debating between heated and cold roller options. While both methods have their uses, the heated top roller of the Widlam L300 provides distinct advantages, especially for specific applications.
Superior Adhesion and Durability
Heated rollers activate adhesives more effectively than cold rollers. When using films with heat-activated adhesives, a heated top roller ensures stronger adhesion. This enhanced bonding increases the longevity of your laminated prints, making them more durable for outdoor or high-traffic applications.
Improved Clarity and Visual Quality
Heated rollers can smooth out any micro-imperfections in the film, resulting in a clearer, crisper finish. Cold laminators might trap small imperfections, leading to a slightly cloudy or uneven surface. For businesses aiming for the highest quality, especially on premium products, heated rollers help produce sharper, more vibrant graphics.
Enhanced Versatility with Different Media
While cold rollers are limited to pressure-sensitive adhesives, a heated roller like the one on the Widlam L300 allows you to work with a wider range of laminating films. From thermal films to pressure-sensitive ones, the ability to adjust the heat gives you more flexibility with your materials. Whether you're laminating posters, vinyl wraps, or banners, you can adjust the heat settings for optimal results.
Faster Lamination Speeds
Heated top rollers also improve the overall speed of the lamination process. Since the adhesive activates quicker, there’s less time spent waiting for the material to pass through the laminator. This means you can take on more jobs in less time without sacrificing quality.
Reduced Silvering Effect
One of the common issues with cold lamination is silvering, which occurs when tiny air bubbles get trapped under the laminate, creating a silver-like appearance. With heated rollers, the adhesive becomes more fluid, effectively eliminating air bubbles and ensuring a smooth, bubble-free finish.
What about applying laminates using a flatbed applicator ? Are there benefits ?
While traditional lamination techniques have their place, more businesses are turning to flatbed applicators, like the Rollover Flatbed Applicator, to streamline and elevate their lamination processes. Here’s why investing in a flatbed applicator can revolutionize your workflow:
Perfect Alignment and Precision
One of the standout features of a rollover flatbed applicator is its ability to provide perfect alignment. Traditional lamination techniques can sometimes result in uneven edges or misalignment, but with the flatbed’s precision control, even large prints can be laminated seamlessly. The flatbed applicator ensures that materials lay flat without bubbles or creases, minimizing the risk of costly mistakes.
Speed and Efficiency
For high-volume print shops, time is money. A flatbed applicator can speed up your workflow significantly. Unlike traditional laminating techniques that require careful, time-consuming hand alignment, the rollover applicator allows for a smoother, faster application process. Prints are laid out and laminated with ease, enabling operators to complete more jobs in less time.
User-Friendly Design
Many flatbed applicators, like the Rollover, are designed with the user in mind. The ergonomic design minimizes operator strain, with adjustable height and easy material handling. For print businesses looking to improve efficiency without overwhelming their team, the intuitive operation of a flatbed applicator is a game-changer.
Versatility
While laminating is one of its core uses, a rollover flatbed applicator can handle more than just films. It can be used for mounting prints onto rigid boards, applying transfer media, or handling complex materials that would otherwise be difficult with standard equipment. This versatility allows your business to take on a wider variety of projects and increase its service offerings.
Reduced Waste and Mistakes
A flatbed applicator dramatically reduces the chances of errors like wrinkles, bubbles, or skewed materials. With the flat surface and controlled application process, you’ll have a higher success rate with each project, reducing wasted material and rework, which translates to better profit margins.
Conclusion
Incorporating a rollover flatbed applicator and utilizing the heated top rollers on the Widlam L300 laminator can significantly enhance both the quality and efficiency of your laminating processes. Whether you’re looking for precision and speed in application or superior adhesion and visual clarity, these tools will elevate your business, allowing you to deliver top-tier products to your customers.
Supportive Content
Video
Here is a video which explains some types of laminates that our available
Blogs
What is self adhesive vinyl laminate
Crystal Laminate | Textured 'Anti Scuff' laminate for extra protection for your self adhesive vinyl
Dry wipe laminate | add something new you your vinyl products
If you would like more information or to speak to a member of our team, please click on the request a call back button below and fill in the small form. Alternately you can contact us on 01948 800379 or email the team on inksandmedia@signmastersystems.co.uk
